Aircraft Fatigue: Causes, Effects, & Solutions
Share this Article:
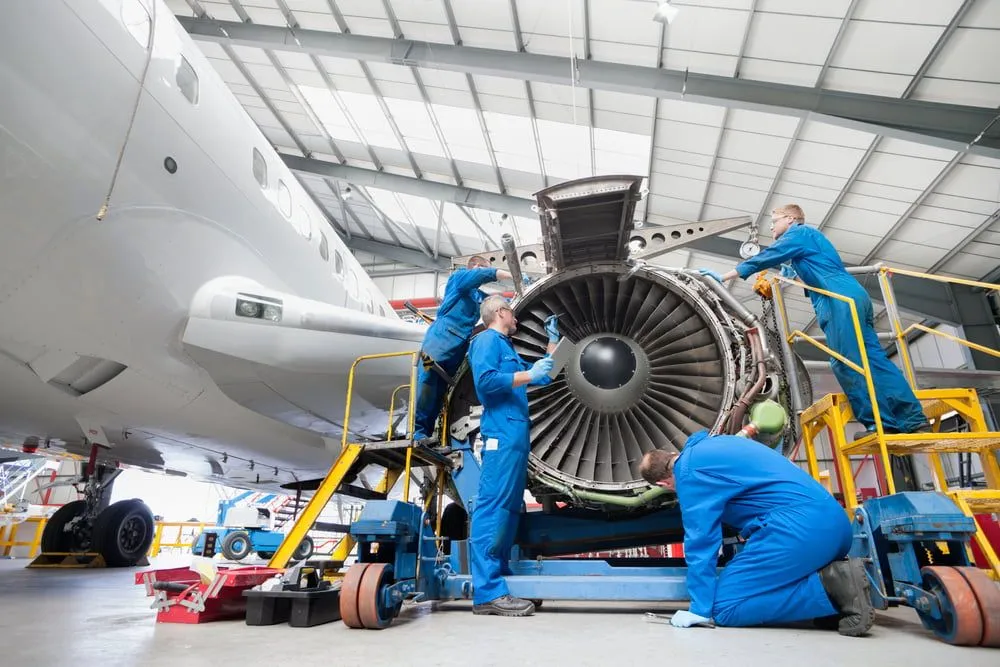
Every part, component, and material has a shelf life. And when that material is regularly traveling tens of thousands of feet above sea level and dealing with various atmospheric pressures and forces, that shelf life might be a little different compared to a material that’s subject to more ordinary conditions.
And when it comes to metals in aircraft, this “fatigue” can be catastrophic and increase the risk of aircraft failure and crashes. So just what is aircraft fatigue and why does it happen? We’ll cover all of that – and more – in this post. Read on to learn more about what you need to know about aircraft fatigue, why and how it occurs, how to prevent it, and more:
What is Metal Fatigue in an Aircraft?
Metal fatigue in an aircraft refers to a weakening in the metal elements of planes, mainly due to repeated flight cycles and the stress on such components over time. This “fatigue” tends to occur in the form of cracks, which begin very small and grow larger over time. Like a vehicle, any new aircraft will age and depreciate as soon as it leaves the hangar for its first flight. As a result, metal fatigue and corrosion begin to occur immediately, though they’re typically not a serious problem until the aircraft can no longer be effectively repaired.
As you might expect, metal fatigue is more common in aging aircraft. It’s why certain aircraft should be retired after they reach a certain number of flight cycles. Failure to do so could present a major safety risk from issues stemming from metal fatigue. Be sure to check with the manufacturer to determine when an aircraft has reached its maximum number of flight cycles, which we’ll also cover later in this piece.
How Does Metal Fatigue Occur?
As we noted in the above section, metal fatigue occurs simply from flying the aircraft over time. Airplanes are subject to a lot of stress flying tens of thousands of feet above sea level. These stresses include atmospheric pressure, G-loads, turbulence, and more. Over time, they’re going to take their toll on the aircraft. Just like a vehicle that has to endure bumpy roads, potholes, and weather events, airplanes have their own fair share of wear and tear that they must endure – and in time, it’s going to catch up with them in the event of corrosion and metal deformities and defects.
Corrosion
Planes are at risk of corrosion as soon as they leave the hangar and take their first flight. Corrosion refers to rusting of an aircraft’s metal parts, often caused by oxygen in the atmosphere coming into contact with untreated metal parts and components. There are various types of aircraft corrosion, including surface corrosion, dissimilar metal corrosion, intergranular corrosion, stress corrosion, and fretting corrosion. Corrosion can be treated. However, if it has become too significant, part removal and replacement is the best option to prevent aircraft failure.
Metal Deformities and Defects
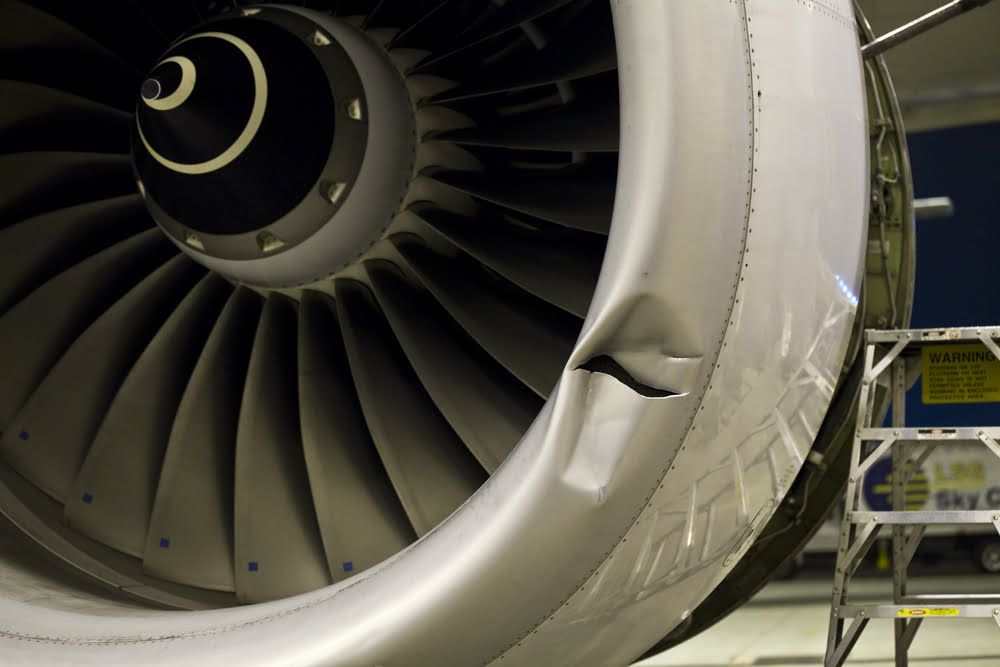
Metal deformities and defects caused by metal fatigue tend to begin in the form of cracks. And while these cracks are so small at first that they can’t even be seen with the naked eye, they become larger over time. Cracks tend to begin in one of three places:
- Internally in structural elements that are placed under high stress.
- Externally in skins under pressure from structural loads.
- At the edges of fastener holes or any area of concentrated stress.
Common Metal Fatigue Failures in Aircraft
In addition to internal, external, and at the edges of fastener holes that we mentioned above, some of the areas that are prone to metal fatigue failure include engines. Generally, any metal part that comes under stress is susceptible to metal fatigue failure – whether it’s an internal or an external component.
How to Prevent Aircraft Fatigue Failure?
The good news is aircraft are required to undergo rigorous testing to prevent metal fatigue – we’ll get into more of that in the next section. And outside of not flying an aircraft, it’s this testing and subsequent repair (if necessary) that serves as the main preventative measure for safeguarding an aircraft from metal fatigue failure. Read on to learn more about the testing requirements and regulations mandated by the Federal Aviation Administration (FAA).
Testing to Determine Metal Fatigue Levels
As noted in the section above, the FAA has developed strict regulations for metal fatigue testing.
The first is determining an aircraft’s Limit of Validity, or LOV, which is defined as the number of hours or flight cycles an aircraft frame can reasonably withstand before it experiences structural failure or metal fatigue. Effective as of 2011, all aircraft manufacturers are required to report an LOV. Aircraft may not be flown beyond the LOV unless approved.
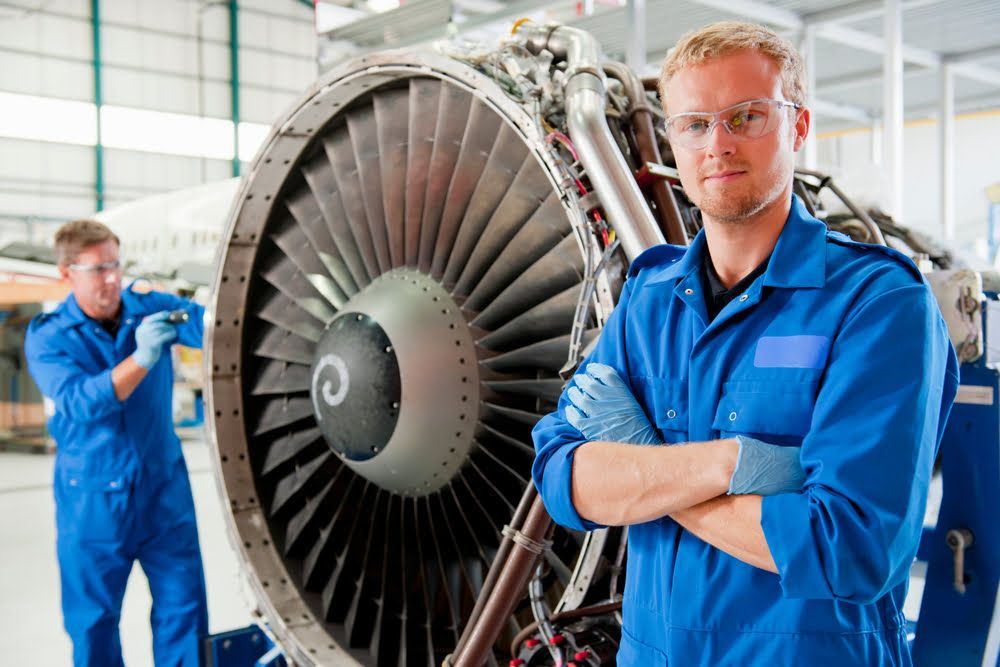
The FAA also requires manufacturers to issue airworthiness directives, or ADs. These ADs essentially serve as guidelines for when aircraft should seek service on various components (i.e., the engine, propeller, etc.). Think of them as manufacturer-recommended maintenance for a vehicle after it hits certain mileage milestones, except ADs are mandatory.
Beyond FAA requirements, rigorous testing is essential to determining metal fatigue levels and ensuring aircraft safety. Corrective actions, such as laser peening and metal polishing, can also be done in many cases to repair issues where fatigue is beginning to set in. At J.A. Air Center, we specialize in aircraft repair and maintenance for just about every airframe and engine and can assess your aircraft for metal fatigue and take corrective action when necessary.
It’s worth noting that these testing, FAA regulations, and repair efforts have made a major difference over time. Currently, it’s estimated that only about 20 percent of all aircraft failures are the result of structural issues. Decades ago, nearly 80 percent of all aircraft failures were due to such issues.